Introduction
KEl’s Stainless Steel Wire for Welding Electrodes Wire are manufactured having excellent mechanical properties, under strict guidance of technical people, diameter from 1.60mm to 5.00mm in Matte & Bright finish and can supply in coil as well as in cut length. The commonly manufacture grades are AWS ER 308, ER308L, ER309L, ER31 0, ER312, ER316, ER316L.
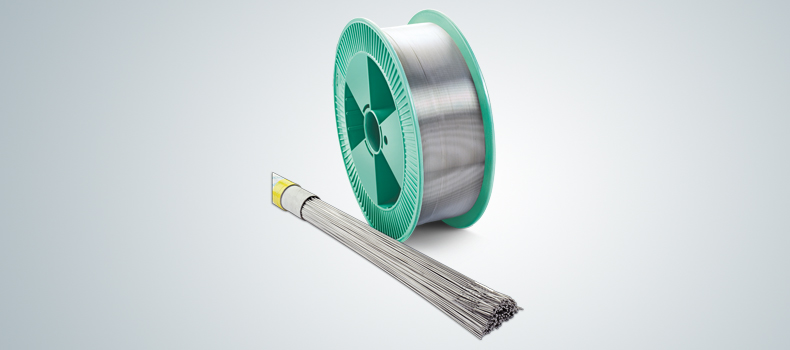
Filler Wire (TIG & MIG)
KEI’s stainless steel wire for TIG in straight length and MIG Wires on spools, layer wound, TIG & MIG Wires are supplied in clean Bright and Matte finish. In grades are AWS ER 308, ER308L, ER309L, ER310, ER312, ER316 and ER316L.
TIG Wire dia from 1.60 mm to 5.00 mm in length up to 1000 mm
MIG Wire dia from 0.800 mm to 1.60 mm in weight spools 12.50 Kg.apx.
When should I use 308L, 309L or 316L,430L filler metal?
308L (including ER308LSi) is predominately used on austenitic stainless steels, such as types 301, 302, 304, 305 and cast alloys CF-8 and CF-3. For high temperature applications such as in the electrical power industry, the high carbon 308H electrode provides better creep resistance than does 308L.
316L (including ER316LSi) filler metal should be used with 316L and 316 base metals. CF-8M and CF-3M are the cast equivalents of 316 and 316L, respectively.
Use 309L (including ER309LSi) when joining mild steel or low alloy steel to stainless steels, for joining dissimilar stainless steels such as 409 to itself or to 304L stainless, as well as for joining 309 base metal. CG-12 is the cast equivalent of 309. Some 308L applications may be substituted with 309L filler metal, but 316L or 316 applications generally require molybdenum and 309L contains no molybdenum.
Type 430 stainless steel filler metal is ideal for 430 base materials because it matches these stabilized grades. CF-8C is the cast equivalent of 430. Type 430 filler metal is also suitable most 308L filler metal applications.
Selecting a Mu to Boost Your Bottom Line
Offshore competition, the increased cost of raw materials, higher energy rates and elevated transportation costs. . . these are just a few of the issues today which are forcing manufacturers to take a hard look at ways to reduce costs and ultimately improve the bottom line.
Because welding can be a significant fabrication activity for many companies, it is usually one of the first manufacturing processes to receive careful scrutiny when cost cutting is the goal. Unfortunately, many manufacturers think that switching to a lower cost MIG wire will be the silver bullet to boost the balance sheet. In reality, an inferior MIG wire could translate into additional dollars spent in pre- and postweld operations such as cutting, forming, surface and joint preparation, pre-heating, cleaning, tacking, grinding and painting.
In fact, when examining the total cost of welding, the cost of the wire is often as low as as approximately four percent of actual welding costs, while the bulk of costs are overhead and labor. So, saving a penny on the price of the wire in the end may actually cost a company much more in productivity-robbing activities that otherwise could be avoided.
Selecting a quality MIG wire is critical. It can bernore forgiving and produce a sound weld even under less than perfect conditions. Take, for instance, a plate with surface contaminants. The right MIG wire for that application may make some pre-welding operations obsolete. And, as more companies move to robotics, a quality MIG wire will provide accuracy in wire placement and consistency in the weld, making rework less of an issue.
The Effect of Wire Diameter
Consistent wire diameter is critical to ensure proper current passage from the contact tip to the wire. Undersized wire causes arcing between the wire and the inside diameter of the tip, which erodes the I.D. of the tip and eventually fuses the tip to the wire. Oversized wire causes excessive feeding force, tip blockage, wire slippage and downtime.
During wire manufacturing, care must be taken to avoid abrupt diameter and cast changes where wire ends are joined together by butt welds. These manufacturing butt weld locations within your wire spool or reel can often cause significant variation in the wire diameter or cast on lesser quality MIG wires. Wire diameter variation over time, even within the AWS specification range, can also affect weld deposition by as much as eight percent. One way to manufacturers can ensure wire diameter consistency and increase your weld quality is to inspect 100% of the wire using laser micrometer inspection methods.
The Importance of Chemical Composition
Be sure to select a wire with consistent chemical composition. Why? Consistent chemical composition results in more consistent performance. Consistent performance will result in greater, more stable quality control. Your operators and weld engineers will more likely be able to set and forget their procedures, rather than re-adjusting to accommodate wire with wildly fluctuating chemical composition.
Here’s something to consider: There are two methods of alloy analysis and control recognized by AWS A5.01. The first, and most common, uses lot control by heat number. A typical heat certification relies on a small sample taken from a heat of molten steel. The resulting heat certification indicates that the chemical composition of the heat of steel is within AWS specifications for its intended use. The problem is that this small mill test sample represents the chemical composition of a huge quantity often 250,000 Ibs. of molten steel.
Also, during the continuous casting of steel, segregation of elements occurs in the ladle from bottom to top as the heat is being cast. Typically, the end of the heat (top of the ladle) will contain steel that has an accumulation of residuals and elements that are not indicative of the rest of the heat. Because a heat certification is an average of the start, middle and end of the heat, there is some probability that material in the heat may contain steel that does not meet A WS requirements. In addition, as different orders are melted at the mill, materials with different chemical compositions can get mixed together. This transition material can alter sometimes significantly the nature ofthe steel.
The second method of alloy analysis and control is by controlled chemical composition. In this scenario, every coil of incoming rod (typically 2,500 to 4,500 pounds of raw steel wire) is tested twice by the electrode manufacturer for chemical composition before being put into production. In this way, the properties in specific coils of steel are matched with qualities that are desirable in specific electrodes and the steel is put into electrode production accordingly. When compared with the heat certification method, this method carries the capacity to allow for additional consistency in chemical composition.
It is also important to note that while AWS provides chemical composition requirements for the finished product, there is no system of monitoring or policing compliance. For some applications, meeting the requirements of the industry for which the application is being produced may be more important than conforming to AWS standards. These industry standards include American Bureau of Shipping (ABS), U.S. Military Requirements (Mil), lIoyds, Bureau Veritas and American Society of Mechanical Engineers (ASME).
Packaging : More Important than You Might Think
With the breadth of packaging options on the market today, selecting the right packaging for MIG wire is an important cost consideration. For example, bulk packaging of 250 pounds and up in drums, reels or boxes can offer many cost advantages. Typically, because there is less handling by the electrode manufacturer, these packages are offered at a lower price per pound.
Specially desirable in robotic applications or heavy-duty semi-automatic fabrication shops, bulk packages make it possible to reduce the number of wire package changeovers per shift or per week. On the other hand, bulk packages can mean increased inventory costs and lost floor space for some shops. Here’s one rough rule of thumb: Some in the industry feel the best price to inventory cost relationship is achieved when the package is depleted and replaced approximately every 30-45 days.
Also, look at shop conditions when considering packaging options. While one company may see cost advantages by purchasing a bulk reel. another manufacturer with dusty and humid shop conditions and/or floor space constraints might be motivated to choose a box or drum which offers full enclosure. In addition, remember that exposed wire is electrically hot when welding. For safety reasons, some shops may prefer enclosed packaging. And while a open reel may be less expensive than a drum or box package, the moving parts of a dereeler can pose a safety hazard. Plus, the dereeler will require ongoing maintenance and upkeep other cost factors to consider.
The cost of disposal is another issue for manufacturers. To save even more, choose a fully recyclable cardboard box that can be crushed down and shredded instead of a wooden reel or metal-rimmed drum. Also, the use of recyclable boxes will aid a company’s compliance in regards to ISO 14001, the latest supplier yardstick in the automotive and other industries.
Items such as lifting straps make it easier for operators to handle the packaging. Also, a wood pallet under the packaging allows for convenient moving via forklift. In contrast, integral paper pallets can be more easily damaged by a forklift. Lastly, select packaging which suits the plant layout. For instance, if some of the welding stations are located on a mezzanine level. it may be more difficult to lift and use some package types into these tight spaces.
Switching to MIG
Up to this point we have been discussing how to get the most from MIG wire. But what if a manufacturer is currently using a stick electrode, cored wire, submerged arc or spot resistance welding? Can a switch to MIG provide benefit in these types of application?
From automotive parts to fabricated structures, shipbuilding, metal buildings and sheet metal applications, all have often reaped benefits from the switch to MIG wire. Advantages include slag free welding with less clean up, even in multiple pass operations. In addition, MIG requires lower operator skills levels than stick or TIG.
Using two MIG wires, called the Tandem MIG TM process, provides lower heat input than submerged arc as well as lower distortion. It is also very versatile and can be used on a wide range of materials from high strength/low alloy metals to advanced high strength steels (AHSS).
Depending on equipment and procedures, MIG has the potential for all-position welding, meaning less fixturing, or positioner, costs. It also has a lower heat input, with the exception of MIG in the spray arc weld mode, for less distortion and burnthough in the finished weld. Other advantages include high electrode efficiency of 97 to 98 percent. In comparison, SMAW offers an efficiency of only 60 to 70 percent because of factors such as spatter, slag coating burn off and stub loss.
Also, solid MIG wire typically has better wire placement than cored wire. Wire placement is the ability of the wire to exit the contact tip in the same location every time for accurate weld placement. This can be an important consideration, especially in automated applications. When comparing MIG wire placement in the joint, look for wire with a consistent cast as a further aid to accurate wire placement.
Conclusion
When looking to reduce overall welding costs, look beyond the price of the wire. Saving a couple of pennies in the short-run, may cost you hundreds of dollars in lost productivity in the long run. Be sure to choose the right wire for a particular application, ensure its chemical composition, and purchase the best packaging option for the plant where it will be utilized. MIG wire quality matters in your overall cost structure. Choose Wisely.
References
American Welding Society. Standard Welding Terms and Definitions. (ANSI/AWS A3.0-94), 1994.